What to Expect From a Transmission Mechanic
A mechanic who specializes in transmissions will be more familiar with your vehicle’s make and model. This specialization increases the likelihood that they will deliver high-quality repairs.
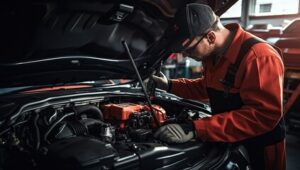
Strange noises such as whining or clunking during shifting are signs that your transmission may need repair. Ignoring these issues can lead to costly problems down the road. Read on for further insights into Transmission Mechanic.
The transmission is a complex component in a vehicle, connecting numerous gears, clutches, shafts, and v-belts to convert energy from the engine to the wheels. As such, its integrity requires close attention and professional assessment to avoid escalation of damage. Warning signs like unusual noises and shifting difficulties are key indicators that it’s time to visit a specialist.
When a mechanic encounters a problem, they first conduct an inspection of the component to identify its cause. The inspection process involves examining all components for cracks, leaks, and other issues that can compromise its functionality. The mechanic then checks for the presence of contaminants in the fluid to confirm that all parts are working properly. The mechanic also analyzes the torque converter for any abnormalities. A faulty torque converter can reduce the efficiency of power transfer, leading to increased fuel consumption and poor performance.
Once the inspection phase is complete, the mechanic replaces any defective or worn out parts. The mechanic selects high-quality parts that meet the model’s specifications, ensuring proper fitment and compatibility. Throughout the replacement process, a technician pays close attention to the application of torque to ensure that all fasteners are securely tightened without applying excessive stress on any components.
Once the repair process is complete, the mechanic reassembles the transmission and runs a series of tests to validate that it operates reliably. During this testing phase, the mechanic pays special attention to operational sounds to ensure that all components function properly. Mechanics also monitor hydraulic pressure and fluid levels to ensure optimal performance post-repair. In order to minimize the risk of injuries, mechanics use ergonomic tools and workbenches that are designed to limit physical strain.
The Input Shaft
The transmission shaft is a key component in the transfer of power from the engine to your car’s gears. It is a hardened shaft with splines that connect to the input gear in the clutch and the main drive gear inside the case. This shaft spins at a different speed than the crankshaft and allows power to be transferred from the clutch to the other gears in the transmission system.
Like all hard-metal components, shafts are susceptible to fatigue failure. The most common mechanism of failure is cyclic stress corrosion cracking (SCC). In this type of fracture, the shaft experiences a high number of cycles in which the stresses exceed its yield strength. The resulting crack propagation region has typical morphologies, such as beach marks, shear lip and radiation zone, which are typically seen in static tensile test specimens.
In addition to cyclic SCC, other failure mechanisms of shafts include deformation failure and fatigue fracture. When a shaft is subjected to rotational bending loads, all points of the surface are subjected to tensile and compressive stresses. In this condition, multiple fracture sources may be generated and expand simultaneously. However, in practice, only one fracture source expands at a time due to the low stress amplitudes generated in this condition.
The failure of this part of your transmission can cause shifting problems in your vehicle, and a mechanic will inspect the input shaft to ensure it is performing as it should. If the shaft is damaged or wearing out, it can become noisy and start to slip between gears. This can be very dangerous for you and other drivers on the road. Ashworth College offers automotive mechanic courses that teach you how to remove, disassemble and reassemble your car’s internal combustion engine, as well as how to diagnose transmission issues. Study online to earn your ASE certification and get on the path to becoming a qualified transmission mechanic.
The Output Shaft
The output shaft is where the power from the gears in your transmission connects to the drive wheels. Depending on the speed you select in your car and the gears your automatic transmission shifts into the shaft spins at a rate that is very close to the desired wheel speed. This allows for smooth shifting and optimal power distribution, which in turn ensures a safe, comfortable driving experience.
The shafts in a transmission are generally quite complex with many different diameters, splines and helical grooves as well as chamfers and through-diametric holes. These features create stress discontinuities that need to be taken into account during design. Couplings can help mitigate these discontinuities but the shaft design needs to be carefully considered as a whole. The cyclic stresses caused by axial shuttle can be significant and this is where accurate shaft alignment becomes more important than ever. A small improvement in angular/lateral alignment can greatly reduce the axial shuttle effect and thus prolong coupling life expectancy.
Shaft flexing is another common problem that can be alleviated by careful shaft and bearing design. The shaft bearings should be designed to minimize bending and torsional loads as much as possible and to provide sufficient clearance for the shaft radial displacements that are inevitable with a flexible shaft. Couplings can also be used to accommodate the axial displacement that occurs with a mechanically flexible shaft. Flexibox membrane couplings offer a non-linear axial stiffness characteristic that dampens axial exciting vibrations.
The output shaft speed sensor is another crucial part of the transmission system. It provides accurate information to the cars computer which allows for seamless gear shifting and optimal power distribution as well as allowing the cruise control system to function properly. Symptoms such as delayed or rough transitions between gears can indicate an issue with the sensor and should be investigated immediately.
The Selector Fork
The primary purpose of a transmission is to manage torque and speed. This process is accomplished via a number of components, which include the main shifting unit that alters the power transmission route from the engine to optimize performance. A key component in this system is the shift fork, which moves a gear collar to engage and disengage various gears.
Essentially, the shift fork is a metal lever with a forked end that straddles a manual transmission gear shaft. This fork is what the driver moves with their stick shift to select different gear ratios in a vehicle’s transmission.
The fork is mounted on a stationary rod and has two prongs that extend from opposite ends of the central plate at right angles to the latter. The prongs are welded to respective support plates that have coaxial through-holes able to guide the fork in a sliding axis which is oriented along the stationary rod (see FIGS. 3 and 4).
One of the through-holes has a wear-resistant bush that is inserted inside the fork, which is able to reduce friction between the actuating nose and the collar. This is an important feature, because the fork is exposed to a significant amount of shifting force that it must be able to withstand.
Oftentimes, this shift fork is exposed to excessive shifting force from the transmission’s clutch when the engine is accelerating and/or decelerating. This can cause the fork to become worn out over time, which will result in a loss of the ability of the fork to move the gear collar and the need to replace it. This is a simple repair for the most part and can usually be done by a professional automotive mechanic.
The Collars
Shaft collars are one of the simplest components found in power transmission. They are ring-shaped metal or plastic components that clamp around a shaft to secure or locate mechanical components. They are used as mechanical stops and to keep sprockets, bearings, and motor components positioned correctly on a shaft. They can also be used to connect the end of a shaft to another part or surface.
The simplest shaft collars use set screws to hold the collar in place. While these do see some use, the screw impingement on the shaft causes marring that makes it difficult to remove or reposition the collar. Modern shaft collars are designed with a clamp that holds to the shaft, and they can be fastened to the shaft using screw-in or socket head cap screws. These screw-in designs are much easier to use than set-screw collars since there is no need to drill into the shaft itself.
Clamp-style shaft collars are available in a variety of styles and materials. The most common are made of steel with a black oxide finish. This coating enhances the screw torque without significantly diminishing its frictional properties with the bore, and this increases the collar’s holding power. Other factors that contribute to a shaft collar’s holding power include its inertia, conductivity, and corrosion resistance.
Mechanics who specialize in the transmission of automotive and commercial vehicles are known as transmission specialists. A transmission specialist has the experience and specialized tools necessary to work on the most advanced parts of the power train, like gears, couplings, and hydraulic pumps. The specialized knowledge required by a transmission specialist helps ensure that the vehicle is running at peak performance and that any issues are repaired quickly and effectively.